February 1, 2018
Pipelines around the world are in danger due to ageing, deposits and corrosion. Leaky fittings and cracks are an environmental hazard. They cause the loss of valuable resources such as drinking water, or put the enviroment at danger by demaged sewer or oil pipes. These problems require a fast treatment.
The replacement of pipes through digging is time consuming, loud, causes traffic jams and has an environmental impact. Trenchless technologies are the perfect solution and provide a modern way to rehabilitate demaged pipe lines.
The main benefits of trenchless pipe rehabilitation compared to other conventional techniques are:
- a shorter construction period;
- a lower burden for neighbourhood residents;
- less traffic disruption; and,
- fewer truck transports for handling excavation and backfill material.
In addition to being environmentally friednly, no-dig techniques usually come at a cost that is below the price of conventional pipe installation projects.
RTi Rohrtechnik International Group is one of the leading specialists in trenchless technolgies. RTi boasts a success record of 35 years and has conducted many successful rehabilitation projects for public as well as private pipe network operators for all types of piping systems, including drinking water, sewerage , gas, oil pipes and industrial pipes.
“Trenchless technologies are an excellent alternative to conventional (open-dig) methods and provide an environmentally-sound solution to restore aging pipes quickly, efficiently and sustainably without digging up the ground,” Edmund Luksch, Managing Director of RTi Asia-Pacific, said.
The Product and Service Portfolio of RTi comprises all technologies used for trenchless inspection, cleaning, repair and rehabilitation of all types of pipes as well as new pipe installations, container/tank rehabilitation, sanitary engineering and landfill construction services. This allows RTi to provide the perfect solution to any problem related to defective gravity and pressure conduits ranging from DN 80 to 5500 mm in size.
There are many innovative techniques like CIPP, Close-Fit and Spirally Wound systems that are used for pipe rehabilitation.
CIPP technology (cured-in-place pipe technology) comprises a variety of hose liners, including relatively simple, PE-coated polyester yarn liners for the pipe interior as well as more complex liner systems for sophisticated static requirements for internal pressure and external loads. In the case of the latter, several needle felt and glass fibre layers are combined. The liners are inverted into the old host pipe by means of a pressure drum by using existing access points to the pipe and cured in place to build a new pipe inside the old demaged pipes. The lifetime of the new pipes can be extended by further 50 years. The construction time can be reduced by more than 50% compared to the conventional methodes.
With the pipe-in-pipe method, pressure pipes as well as gravity pipes of various diameters and lengths can be rehabilitated cost-efficiently and quickly. The Close-Fit method is based on an HDPE pipe, which is extruded and then shrunk in diameter by using thermo-mechanical tools. With its diameter reduced by 25-30%, the new pipe can be easily pulled into the damaged host pipe. Even construction pits of 950 metres in length are manageable as pipes are wound around drums and pulled into the host pipe by means of a force-locked hoist. Hot steam and pressure mould the HDPE liner into shape, so it forms a close fit with the host pipe. Luksch explains: “A close-fit pipe has the same properties as a new PE pipe. It can be connected to the piping system through standardised PE fittings.”
For more than 30 years RTi Group members have been developing and applying these modern technologies to upgrade ageing infrastructure. RTi is represented in Australia by its own company, RTi Asia-Pacific, and is based in Adelaide.
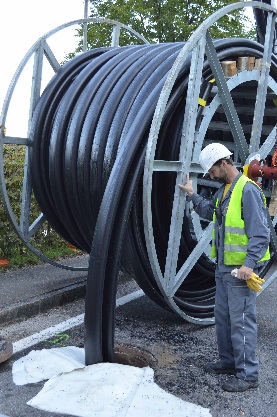
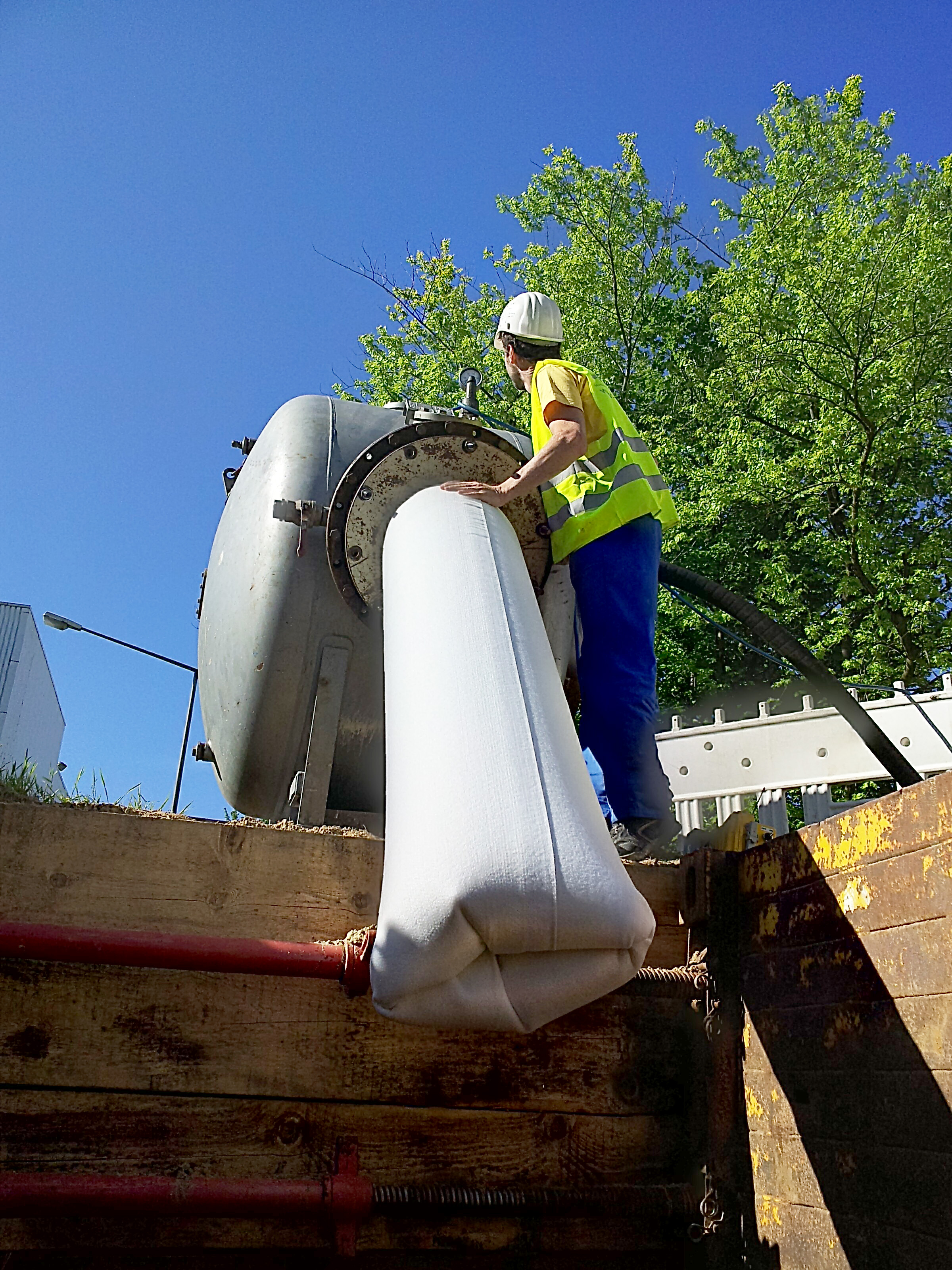